Electric vehicles (EVs) are a thing of the future. The more countries pledge to phase out the registration and sale of internal combustion engine (ICE) vehicles, and the more consumers spend on EV purchases year-over-year, the more the global automotive industry shifts toward electrification. This transition bodes well for decreases in greenhouse gas emissions (GHGs) and an overall improvement in fuel economy.
That said, there are presently no regulations regarding EV battery end of life. The lack of firm policy frameworks for the restructuring of the EV battery industry, in terms of material sourcing, implementation by the original equipment manufacturers (OEMs), and traceability throughout the supply chain, risks creating an electric car battery disposal problem that undoes the ‘greenness’ of electric mobility.How Big Will the Electric Vehicle Market Become?
As it stands, EVs account for a small portion of the market. There were only 10 million vehicles worldwide in 2020, mostly concentrated in China and Europe, making up a paltry 4.6% of the world’s passenger car sales and 1% of its cars.
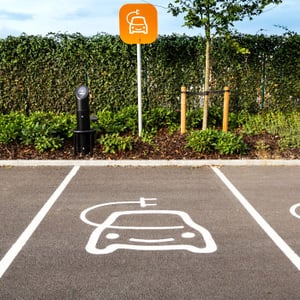
However, every major car manufacturer has at least one electric vehicle in production, and 18 of the 20 largest OEMs—when combined, roughly 90% of all new car registrations worldwide—have committed themselves to increasing the supply of EVs. Some, like Toyota and General Motors, even plan to reconfigure their product lines to phase out all ICE vehicles. Consumers, in turn, are buying more and more: in 2020, they spent upwards of USD 120 billion, representing a 50% rise in a single year.
Beyond the increased supply, electric cars are gradually becoming more competitive. Their driving range is improving, their charging time is constantly shrinking, and their total-cost-of-ownership is decreasing thanks to strong investor enthusiasm, private sector demand for low-emissions commercial fleets, and fiscal incentives (such as the EU’s 2020 subsidy scheme to buffer EV purchases from the COVID-induced downturn).
Overall, the market is growing, and it is expected to keep growing until reaching a worldwide tally of 125 million EVs by 2030.
The Problem with Electric Vehicle Batteries and Their Supply Chain
A projected rise in the uptake of electric cars is bound to carry over into EV battery demand. OEMs wishing to secure the supply chain for future EV sales are increasing investment, intensifying raw material extraction processes, and driving the price of batteries down, thereby incentivizing demand. Lithium-ion (Li-ion) battery production, which makes up more than 70% of the rechargeable battery market, went up by one-third last year; its price, on the other hand, dropped to USD 110 per kilowatt hour (from USD 1,000 in 2010).
If this trend continues, global EV battery production would grow fourteenfold. An upsurge of that magnitude entails scaling raw material mining and refining, cell production, and EV battery recycling up to 25 times what they are today.
Beside the pollution from raw material sourcing and the release of GHG emissions during battery manufacturing and energy production, such growth is problematic since Li-ion batteries are not recyclable in the same way, say, lead-acid car batteries are. Given that they lack a standard chemistry and manufacturers are not required to disclose their specific compositions, would-be recyclers are often dealing with metals and parts they cannot process or resell. They generally extract about 50% of the battery’s materials; the rest is dumped, incinerated, or exported to countries with weaker standards.
Moreover, recycling is not profitable: the cost is often greater than the value of the lithium retrieved. Without financial incentives to make up the difference and regulations that extend producer responsibility to the entire electric battery supply chain, including collection and recovery, we will continue recycling at most 5% of Li-ion batteries.
That recycling rate might not seem like a big issue now, but when we consider that by 2030 11 million metric tons of batteries will reach the end of their service lives and become waste, it turns into a ticking time bomb.
Even though more stringent legislation is sure to follow the growth in EV supply and demand, we cannot expect a policy overhaul to single-handedly multiply recycling rates, least of all in less mature markets like the United States. For this reason, OEMs, public partnerships, and researchers are taking matters into their own hands and searching for cost-effective ways of making batteries more recyclable and of taking greater ownership over their supply chain, such as by vertically integrating battery production and recovery.
EV Battery Passports, Life Cycles, and How Software Helps Recycle
The Global Battery Alliance estimates that a sustainable and circular battery value chain would contribute 30% of the emission reductions that the Paris Agreement requires from the transport and power sector.
According to them, this shift would not be possible without a “battery passport” to ensure consistency and transparency. They define the battery passport as the digital twin of the physical battery that documents its movement along the supply chain, from raw material mining to recycling and re-entry. A demonstration product is in the works; similarly, Ford, the US Department of Energy, and Australian startup Everledger are teaming up on a pilot program that uses the Internet of Things (IoT) to keep watch of EV and portable electronic batteries.
At the same time, ERA has already spent a couple of years building a prototype of an EV battery management module to track materials at the chemical level. The software would assign smart tags to the components (battery cells and complete packs) and store the information on their material compositions from the moment a supplier delivers them to the assembly plant, or when the OEM builds the battery pack on-site. Qualified stakeholders would then scan the tags and access a distributed ledger on the cloud, or blockchain, where they can monitor the battery’s location, condition, and health at every step of the supply chain. At the end of the battery’s life, the recyclers, equipped with a record of the battery’s history and chemical breakdown (so they know what to work with), can recycle the raw materials, repurpose the main components, or recover the metals and sell them separately.
All this data would be uploaded electronically in the form of a safety data sheet (SDS) into ERA’s dynamic platform and kept for as many as 25 years—longer than the average electric car battery’s lifespan (up to 20 years). Ultimately, suppliers, OEMs, and recyclers would have the tools to manage the batteries in line with the regulations that governments worldwide are gradually adopting to fight the impending spent-battery waste situation.
ERA's Battery Management Through Blockchain
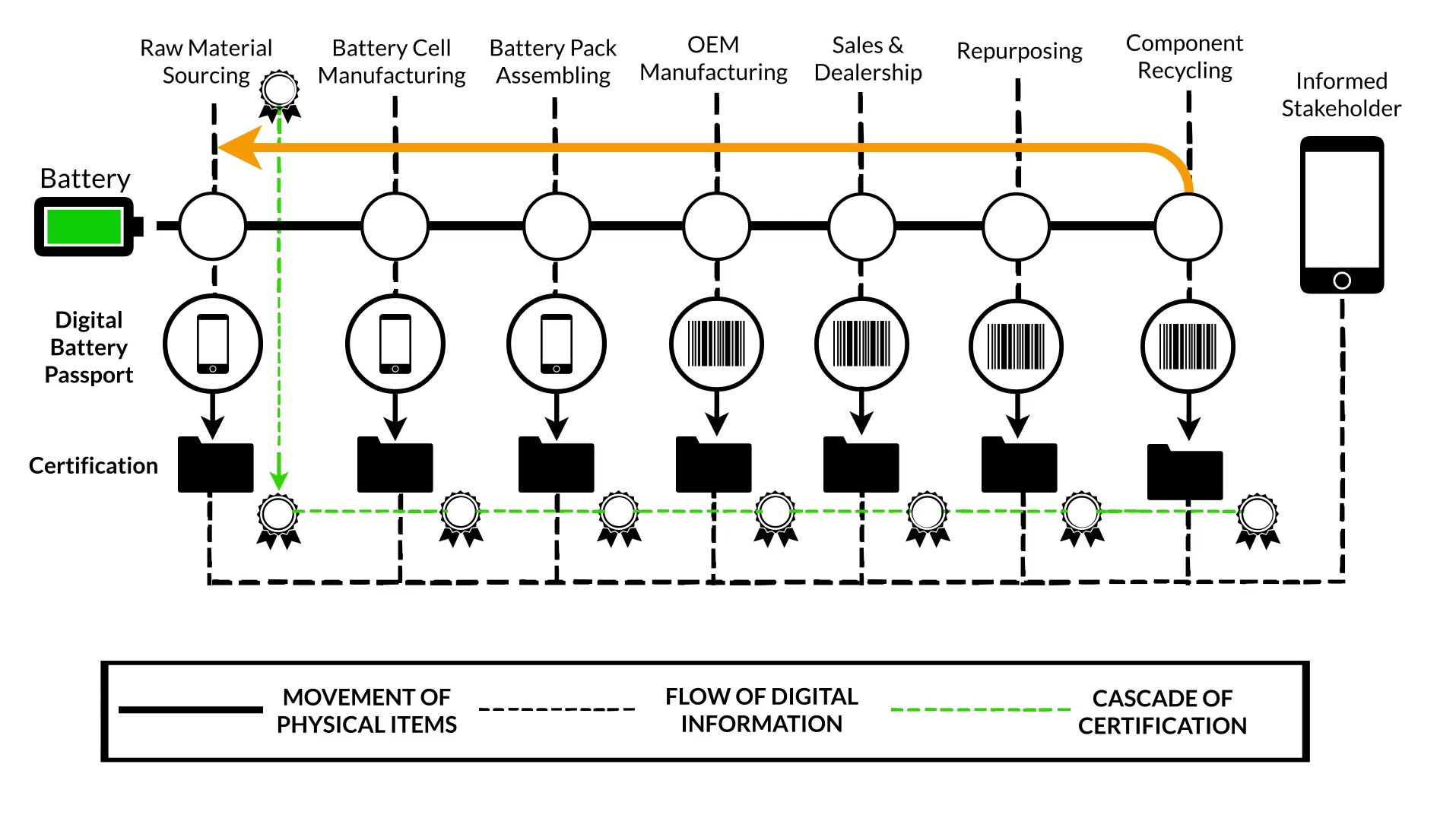
OEMs are just starting to modify their assembly plants to build EVs. General Motors (GM), for example, is investing USD 35 billion in EV product development between now and 2025. We can expect GM and companies like it to shore up their financing with recovery and circular economy measures, which is why ERA’s battery management module, despite being a prototype, is ready to be switched ‘on’ and trial ran when needed. In fact, Nissan is already using the EV battery materials tracking capability for recordkeeping and compliance purposes. Other OEMs like Toyota, Stellantis, BMW, and Volkswagen, to name a few, have been working with ERA’s Environmental Module and EHS software to map out their entire production processes and simplify chemical usage recordkeeping.
Watch the video below to learn more about ERA’s commitment to a responsible and sustainable battery value chain.
The SP's Responsible Battery Work Group and Shining Star Award
The software capabilities just highlighted are the fruits of ERA’s co-founder and co-CEO Gary Vegh’s efforts to make the most of his involvement with the Suppliers Partnership for the Environment (SP).
Gary owned an EV for seven years prior to joining the SP’s Responsible Battery Work Group in early 2018. Considering where his vehicle’s battery would end up, he found a way of adapting ERA’s software to provide the automotive industry with a tangible, cost-effective solution to its recovery and recycling problem. The positive response he received upon presenting this solution to his fellow SP members—composed of automakers, suppliers, recyclers, and waste companies—is perhaps best demonstrated by the Shining Star award, which he won in late October of this year. SP recognized his leadership, long-term engagement, and active support of environmental sustainability initiatives, citing his contributions to battery-tracking innovation and waste minimization as examples. But his work is far from over; Gary is always looking for the next sustainability measure to design and put into practice!
End of life management is growing increasingly important in all industrial sectors working with rechargeable batteries, and solutions like Gary’s are bound to become more prominent with time. Schedule a call with one of our analysts to discuss your materials tracking and compliance options going forward.
Tags:

December 13, 2021
Comments