Compliance with the Globally Harmonized System (GHS) is about more than just authoring SDSs (Safety Data Sheets) and making sure your staff knows how to read them, it also includes an important component about ensuring that safety data is available throughout your facility on any secondary containers used to store a hazardous material.
Definition: A secondary container is defined as any container holding a product which is not the original container supplied by the manufacturer.
The United States and Canada comply to separate entities with different applications of the GHS standards. In the U.S., the 2012 Hazard Communication Standard (HCS) is used and in Canada, the Hazardous Products Regulations (HPR) was established. There a few differences in label requirements and knowing the differences between the two systems and how to apply their corresponding secondary container labels is paramount for any safety professional.
The common causes of incidents or health effects that can be traced back to secondary container labels include:
- The material not being used within the same work shift as the person who made the transfer from primary to secondary container.
- The person who oversaw the transfer leaving the work area.
- The secondary container itself leaving the work area to a location where it cannot be correctly identified.
Secondary Container Labels in the United States
In the US secondary container labels are required when operations in a work-place setting includes the transferring of smaller amounts from the original container to a secondary container such as a beaker, flask, or bottle.
These secondary labels need to comply with OSHA’s HCS. The standards are in effect to prevent any cases where uncertainty of the handled material could jeopardize the health and safety of anyone on site. However, secondary workplace labels are not needed if the transferred product is used up in its entirety by the person handling it with in the initial work shift. All original labels cannot be removed, altered, or defaced and if a replacement label is needed, no information can be omitted from the first to the second label.
There are two mandatory pieces of information which need to be included on the Secondary Labels: the identity of the hazardous chemicals within the product and the hazards, either physical, health-related, or environmental, the components present. The HCS requires that the specification of pictograms, signal word, hazard statements, and precautionary statements must be included on all primary labels [PDF].
Regarding hazardous material which are stored in ampoules/bottles which are too small to affix the required HCS 2012 labels, OSHA recommends that labels can be modified as a pull-out or fold back styles, as well as formatted as tags. There is no exception where a package containing smaller vessels of hazardous material may be labeled instead of its contents. As they both should be labeled in tandem, the very minimum label requirements, in the case the vessels are indeed to small, would be a sticker with the product ID, appropriate pictograms, the manufacturer’s name and phone number, the precautionary Single Word, and a statement indicating the full label information for the chemical is provided on the outside package. The outside package must, in turn, contain the remaining information requires by HCS 2012.
Failing to comply will result in OSHA fines.
Secondary Container Labels in Canada
In Canada, the WHMIS 2015 legislation requires that all hazardous material in the workplace must be labeled accordingly. The responsibility for proper hazardous product labeling generally falls on the supplier of the product. However, employers are responsible for making sure that hazardous products are labeled appropriately when coming into their workplace and maintained when being stored and used.
Employers are also held accountable for ensuring that adequate workplace labels are applied to a hazardous product which is:
- Made and used within that facility,
- Opened and transferred or poured from its original container,
- And lastly, a supplier label becomes lost or no longer legible.
Information on the workplace label must include the three following criteria:
- The product name in the exact form it is found on in the Safety Data Sheet,
- Safe handling precautions which could be in the form of pictograms or in the same format as the supplier label information,
- And a reference to the products Safety Data Sheet, if available.
The only two reasons a workplace label may not be required is if an employee transfers a hazardous product and uses it immediately or if the product remains, "under the control of the person who decanted it" according to CCOHS. This means that the person who transfers the product from its original container ensures it will be used in its entirety during that one shift and kept always with in their proximity.
It is important to note that although a workplace label is not required, the vessel must still be clearly identified. In specific cases, a WHIMIS label can be portrayed as a mark, stamp, sign, sticker, seal, tag, ticket, or wrapper imprinted or adhered to the container. The situations to which these exceptions can apply are:
- In cases where bulk shipments are purchased or where products are sold without packaging.
- Containers of 100 mL or less, where only the hazard statements may be exempt.
- Containers of 3 ML or less, where a label would hinder the normal use of a product- a legible shipping and storage label is still required during the use of such a product.
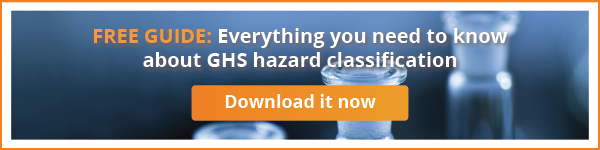
Notable Differences Between the Two Countries
Although there is great similarity between the two countries, each hold their own set of regulations. The key variances between Canada’s WHIMIS and the US’s OSHA workplace label requirements pertain to the following:
- Language: in Canada both French and English are mandatory, the US only requires an English version.
- Supplier identification: where a Canadian importer may retain the name of the foreign supplier rather than replacing it with their own if the hazardous product is imported for use in their own work place (according to Health Canada), the US must provide the name, address and telephone number of the U.S. manufacturer, importer, or other responsible party.
- Mixtures containing a Category 2 Carcinogen at a concentration between 0.1% and 1.0%: where all mixtures classified as Carcinogen Category 1 or 2 between the aforementioned ranges are require to have a label and SDS; the US only requires such a mixture classified at Category 1 Carcinogen to have an attached label.
Moving Forward - HazCom 2012 Labels and NFPA/HMIS
Older labeling requirements for both shipped containers and workplaces, pre-HazCom 2012, were generally performance-based. This means that OSHA’s requirements were not black and white. The contents of the label were subjective, and the primary objective was that the relevant hazard information be displayed to the end user. As a result, the HMIS and NFPA symbols were broadly adopted. Both were able to neatly display hazards within a material such as health effects, flammability, reactivity/hazardous physical properties, and recommends personal protective equipment.
The colors are designated to each section; blue- Health, red- Fire, orange-Physical and the number scale was simply spread from 0 (least concern) to 4 (highest concern).They could be used individually or in conjunction, portraying an accurate picture of what users would be handling and what sort of precautions must be taken.
The HMIS and NFPA standards have still been used avidly around the workplace, even with the HazCom 2012 updates. However, for anyone using these systems, you need to be aware that the HMIS and NFPA, while still accepted by OSHA and throughout the USA and Canada, is quite literally getting inverted. All previous ratings were scaled 0-4 but now the GHS system is using the scale 1-5, with 1 indicating a severe hazard and number 5 indicates a minimal hazard. The scale is inverted numerically - a low number and a high number now mean the same thing - which may render NFPA and HIMIS no longer relevant or even a source of dangerous confusion.
As both entities, OSHA and WHMIS, aim to better convey the risks involved with shipping, storing, and handing hazardous material, they are also taking the necessary strides to ensure compliance with the UN’s Globally Harmonized System. Not only will this unify how such hazards are conveyed to the end user, it opens the doors of open communication, proper on-site training, safety measures, and an overall better understanding in general of the handled materials. Labels provide a to-the-point message of the dangers which may arise from using such a product but also instill a sense of security at the same time – one that all safety precautions are being conveyed and all necessary steps have been taken to ensure that the user’s safety has been made precedent.
Getting Started
If you haven't started authoring secondary container labels for your workplace yet, it can seem like a daunting task. After all, the frequency at which you need to author or reauthor labels can be intense depending on the type of work you perform and how you currently store or transfer materials on site.
Our advice is to make sure whatever authoring system you use is able to simultaneously create a secondary container label for any material at the same time you author a full SDS. so if you are creating SDSs by hand, take the time to create a secondary container label template that will allow your team to create future labels on the fly - ultimately saving you time.
Even better is to use a system that automates the entire SDS authoring and Secondary Container Label authoring - one chemical database, built-in templates, complete hazard determinations, and the full library of GHS pictograms. This will let you author a full 16-section SDS and container label in under 5 minutes - with reprints and updates done on the fly in just moments. This means you can create a full suite of digital secondary container labels available to anyone on your team who needs to store or transfer a hazardous material.
ERA's SDS Authoring and Management system delivers all of these benefits, while making your chemical management more cost effective and freeing up your time.
Our chemical researchers have written a free ebook about the GHS that will walk you through the process of GHS compliance. Download your free copy today and share it with your coworkers.
On-Demand SDS Authoring Webinar
Want to learn more about what goes in to each section of an SDS and how the information plays a vital role in preventing injuries and mitigating risk? ERA is providing an on-demand free webinar that will give you a deep-dive into SDS sections, SDS authoring, and how it all relates to Health & Safety compliance.
- Differences between OSHA, CLP, and WHMIS
- Dos and Don'ts for SDS Authoring
- How to keep up with changing GHS standards around the world.
Click the button below to access the on-demand SDS webinar.
This Blog was Co-Authored By:

September 11, 2017
Comments