Meeting the standards and regulations of OSHA can be complex and challenging for companies to manage. But the cost of noncompliance is not only monetary; it can also risk the lives of employees. No matter how challenging it can be doing regular safety inspections, the cost is too great to take any chances. If you’re reading this article, it means you understand how important it is to have effective safety auditing processes in place and you’re looking to improve things at your work sites.
The Importance of OSHA Inspections Preparation and Response
This article deals with a real-world case study of a business that was recently cited by OSHA for 12 safety violations following 4 employees suffering from fatal injuries resulting from an explosion. The business and all associated persons will remain anonymous, but we will take a realistic look at how the safety management for that facility could be improved so that you can take a preventative approach to similar incidents. For the sake of this article, we’ll call the business in question “Company X”.
OSHA provides rules in a multi-part document called the 29 Code of Federal Regulations (29CFR) that applies to general industry and is commonly used in inspections. The 29 CFR 1910 Subpart B OSHA inspection process assists companies in distributing safety plans to improve workplace safety and provides a firm backbone for any inspection program. The point of this regulation is to enforce practices which, when followed, minimize the health- and life-threatening risks found in many workplaces. In the case of Company X, the violations cited were deemed preventable and if there were a system in place to manage the inspections and range of safety activities applicable, perhaps the story would have ended differently.
So, what can we learn from Company X and how to improve safety inspections? Here are 4 steps to improving your OSHA inspection reports that your business produces and keeps in house to assess and document safety:
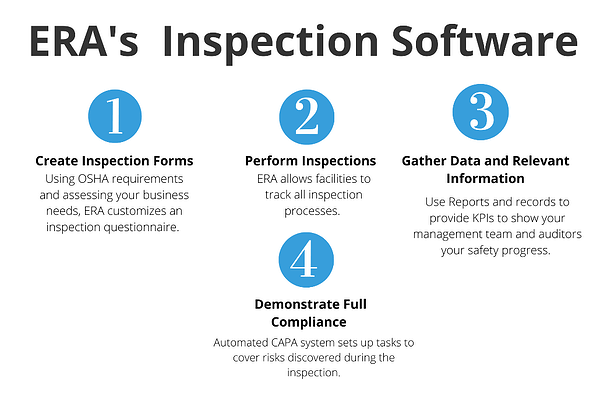
1: Create Inspections Goals and Track Your Progress
In the citation for Company X, OSHA cited the electrical wiring and flammable liquids near where employees handled and processed volatile liquids and gases—causing an increased chance of ignition. The first step of any OSHA inspection process would be to assess the workplace risks and determine which parts of the 20 CFR regulations deal with Company X. The applicable OSHA subparts for Company X include:
- 1910 Subpart E/ Exit Routes and Emergency Planning/ Fire prevention plans
- 1910 Subpart H/ Hazardous Materials/ Flammable liquids
- 1910 Subpart S/ Electrical/ Wiring design and protection
Using these OSHA subparts, we recommend compiling your workplace safety requirements into a centralized form to determine the applicable hazards and safeguards you must have to be OSHA compliant. ERA does this seamlessly with inspection questionnaire that pulls from the CFR 20 Standard to create a safety program and a CAPA (Corrective and Preventative Actions) system.
Once you have progress on your compliance, you can specifically target the areas where you are falling behind and keep a record on all your corrective actions and associated tasks. Having a clear set of standards and rules can also help you perform inspections and other safety measures like Behavior Based Safety Observations or audits to close compliance gaps and figure out the specifics of your workplace shortfalls at a given time—whether the mistakes taking place are human or process errors.
Inspections are vital to this process as this can show OSHA inspectors that you are making a good faith effort to improve safety. Tracking and recording the inspection progress, failures, and corrective actions give regulators the transparency they need to measure the compliance of your facility.
2: Perform Your Inspection
In the example of Company X, we demonstrated how one could customize their workplace hazards using the OSHA CFR Standards and create OSHA inspection forms to perform effective inspections and audits in order to assist employees in delegating tasks tied to their inspections. However, there are more important things to glean from inspections; inspection KPIs reveal the level of compliance with each OSHA standard and applicable documentation and photos also reveal the level of non-compliance and the severity of the potential hazards.
We suggest using a standardized form or OSHA inspection checklist - the 29can provide the standards you need to follow. Following standards is a far superior method of building and performing audits, since you'll be following OSHA inspection procedures rather than guessing. ERA software uses a combination of dynamic forms and built-in standard OSHA inspection forms to give you a library of 29 CFR forms you can easily complete as well as the ability to create custom forms where desired.
3: Gather Inspection Data and Assess Your Risks
When hazards uncovered during an inspection are discussed, organizational risk is an important factor to consider. Deciding the corrective measures needed must be the priority and is best managed through the lens of risk. ERA recommends you employ the use of a risk assessment matrix as a data point to organize all an organization’s risk and set priorities.
This risk matrix shows an example of a risk breakdown by impact area, probability of occurrence, project impact, risk rank, and risk controls.
Of the cited OSHA Hazards from Company X, below are the risk rankings:
- High Risk: Electrical wiring and equipment were not safely installed where flammable liquids were handled, processed, or used;
- High Risk: The equipment and wiring methods used were not intrinsically safe, approved for use around flammable liquids, or safe for a location classified as hazardous;
- High Risk: Locations where flammable vapor-air mixtures may exist under certain conditions were not properly classified; and
- High Risk: Forklifts powered by liquid propane were used to transport volatile flammable liquids and operated in areas where employees handled and processed volatile flammable liquids and gases, creating the potential for ignition.
After an inspection, the best way to manage findings and set intelligent priorities is through combining data from inspection findings and tying them into risk assessments to provide a clear path for future workplace safety.
4: Demonstrate Your Compliance with OSHA Inspection Standards
Companies with safety hazards must have a record of training, audits, and inspections to show regulators efforts made to ensure workplace safety. Through the use of Inspection Software, Company X could have populated records to show OSHA regulators their safety record from inspections to training sessions that occurred as a result of OSHA inspection findings. Even if the inspection record reveals many shortfalls, OSHA regulators will sometimes adjust penalties based upon the good faith of the employer. This is when recordkeeping is key.
Having an automated system in place that houses all your inspection data in a centralized platform is the easiest way to handle the myriad of tasks, regulations, communications, and recordkeeping necessary for full compliance. For employers to improve and maintain safety on the job, we recommend that they utilize software designed to prevent compliance errors and manage their tasks. That’s why Inspection Software is key. It provides the first line of defense for all compliance shortfalls while providing the most valuable compliance improvements.
Free Risk Assessment Strategy eBook: Get it Now
Because introducing a safety culture is so important to any workplace, we're providing everyone in the H&S field with a free eBook to help explain the best practices for a workplace Risk Assessment Methodology. It's designed specifically to help with Root Cause Analysis processes and to help you figure out which risks to prioritize. Download the eBook now.
This Blog Was Co-Authored By:
Tags:
EH&S Inspections
April 9, 2020
Comments