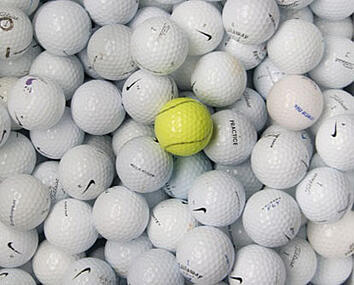
There's lots of discussion in growing industries about the best ways businesses can improve their environmental compliance, without sacrificing profitability or efficiency in the process. One method getting serious attention right now is the idea of Environmentally Preferable Purchasing (EPP). But how does picking "the green option" give an advantage without sacrificing profitability or efficiency?
If you’ve never heard of the concept before, start by reading a the EPA's description. In essence, environmentally preferable purchasing (EPP) is all about front loading your environmental management by knowing the environmental impact of your materials before they even enter your facility.
The central idea of EPP is straightforward: the materials that you bring into your facility and use to make your end products dictate almost everything else that happens in your product life cycle.
All your waste, air emissions, greenhouse gases, and environmental compliance reports can all be tracked down to the raw materials you purchase.
How to control your emissions before they're generated
Are your emissions higher than your permit allows?
Maybe the solution isn’t to scale back your production schedule but instead to re-evaluate was sort of coatings you’re using.
Are you spending a fortune shipping waste off to a treatment facility?
The problem might not be how efficient your processes are, but how environmentally efficient your raw materials are.
Are you slowing down production because your work staff uses a lot of sick days?
It might be time to examine the health effects and best-practice rules around your materials.
Do you often have to pay fines or work to correct noncompliance situations at your facility? Are you fixing the symptoms and ignoring the cause(s)?
Environmentally preferred purchasing could be the answer to all these problems.
Sound far fetched?
Let’s take a closer look:
- It is always more expensive to make a mistake, get caught and be made to fix it than it is to prevent the problem ever occurring. The EPA will charge you with fines on top of being expected to clean up any spills or accidents you caused.
- Air emissions have an undeniable effect on sick days and worker productivity. Of course, it’s difficult to quantify exactly how much of an impact your materials have on workers’ health, but there’s a reason the EPA always justifies any new regulations by estimating the amount of money saved by reducing or preventing sick days and missed work.
- A material that generates no toxic waste is dramatically easier for a facility to manage at the end of the manufacturing process. You reduce the cost of shipping the waste off for treatment, or might even be able to simply recycle or reuse the material if it’s green enough.
Implementing Environmentally Preferable Purchasing at your Facility
In principal, environmentally preferable purchasing could be the solution to a lot of problems and is an essential step in getting a sustainable supply chain. But definitely do not underestimate the amount of work that EPP can take.
Evaluating one material alone can take an environmental manager a lot of time, since it requires building theoretical production schedules and estimating air emissions and waste generation. If you were to completely overhaul every material in your chemical inventory, it could become quite the burden and compromise your ability to perform other necessary tasks.
That’s why forecasting has become such an in-demand feature for chemical inventory management tools.
It can take the guess work out of environmentally preferable purchasing.
To ensure success, the Practice Greenhealth organization website has a few tips for EPP material management that could be useful at your facility, including:
- Make it a team effort
- Make EPP a formal program at your site
- Start small then expand
Check out more of their tips.
ERA is a firm believer in automating your environmental management as much as possible, and this goes from environmental preferable purchasing too.
Why not check out our free eBook on data automation to learn more?
Image credit: mudeth
Tags:
Compliance
July 2, 2012
Comments